功能安全流程
汽车产业中功能安全开发程序的实施遵循 IATF 16949 和 ISO26262 标准。将功能安全程序纳入立锐汽车开发流程中对符合行业标准、确保产品的安全性和可靠性至关重要。通过与汽车产品质量计划(APQP)、安全计划、实施安全分析、确认措施和安全案例文档,我们为专案中的功能安全奠定了坚实的基础。
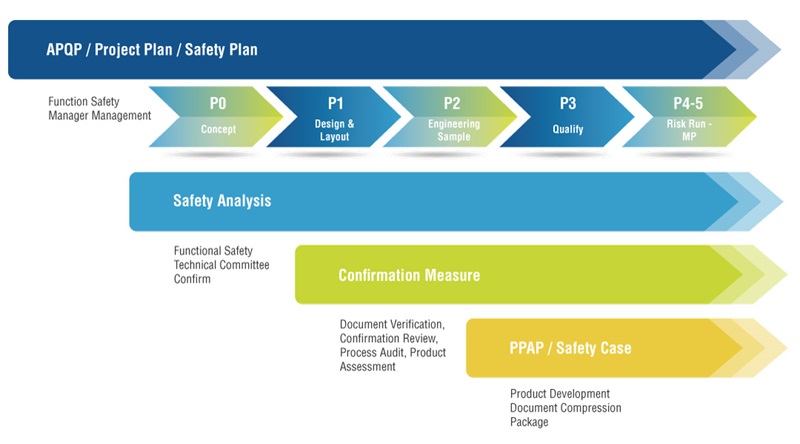
APQP/Project Plan/Safety Plan:
功能安全开发流程的基础建立在 IATF 16949 和 ISO 26262 标准之上。我们的项目计划和安全计划与汽车产品质量计划(APQP)框架保持一致,这是一个针对汽车产品的全面质量开发计划。这确保了将安全考虑纳入专案的所有阶段。
Phase 0 - Concept:
概念阶段是对精确性需求最高的阶段,因为容易发生人为错误。这个阶包括:
- 定义每个参与者的角色。
- 收集来自客户的安全需求。
- 提出系统的安全概念。
- 审查整个流程和安全计划,确保组件准备好进行设计。
Phase 1 - Design and Layout:
设计阶段用于验证所有功能方面。主要包括:
- 管理所有与安全案例相关的工作。
- 释放安全计划。
- 执行与假定的系统安全概念一致的安全设计。
- 进行失效模式和影响分析(FMEA),以减少 IC 功能和安全机制之间的常见故障。
- 执行定量安全分析(FMEDA),确保 IC 设计满足功能安全指标(PMHF、SPFM 和 LFM)。
- 确保所有开发工具分类并符合 ISO 26262 标准。
- 如果项目涉及 IP 使用,进行硬件影响分析和风险评估。
- 通过模拟验证定量安全分析中定义的诊断效果。
- 分析单点故障和常见故障的模拟结果,包括封装故障分析和定性分析。
- 通过内部独立团队管理审核安全案例的流程。
Phase 2 - Engineering Samples:
- 该阶段涉及获取组件的过程。管理外包制造商符合汽车等级要求的合规性。这些信息由功能安全经理验证,任何偏差都需要立即审查。
- 对所有安全设计机制及其相关诊断范围进行质量验证。
- 通过设计验证和确认阶段完成组件测试和验证。
- 测试涵盖 Alpha-site 电气验证、AEC-Q100 封装可靠性认证和自动测试设备(ATE)生产测试。
- 内部独立团队对安全案例和流程管理进行确认和审查。
Phase 3 - Quality:
- 所有安全设计机制及其相关诊断范围均包含在质量验证范围内。
- 发布全面的 AEC-Q100 可靠性认证报告。
- 更新安全手册和安全分析报告。
- 评估功能安全设计是否符合系统设计定义和 ATE 生产测试(CP/FT)。
- 第三方功能安全评估,以确保设计的安全符合产品规划和假定的系统应用。
- 内部独立团队审查安全案例,在获得批准后完成安全案例。
Phase 4 - Risk Run Production:
- 遵循汽车开发流程标准执行所有监测和评估测试,并评估测试覆盖率后,产品可以进入量产阶段。
- 功能安全经理和指定的协作人确认所有与安全相关的审查,以及所需的评估或测试。
- 在安全案例中记录所有安全论点,并档案保存超过 15 年。
- 内部独立团队进行功能安全认证,并在完成和发布产品的安全案例之前审查功能安全案例,以使产品进入量产阶段。
Phase 5 - Mass Production:
Safety Analysis:
为确保我们安全措施的坚固性,所有功能安全分析文件都经过独立单位的严格审查流程。这种统一的安全审计包括关键分析,如失效模式和影响分析(FMEA)、故障树分析(FTA)、设计失效分析(DFA)以及失效模式、影响和诊断分析(FMEDA)。
Confirmation Measure:
开发过程的每个阶段,从 P0 到 P5,都符合安全措施的要求。所有程序,从需求定义、规范、测试到生产,都经过了彻底的验证。此外,内部独立单位已对产品的功能安全设计进行了功能安全审计和评估。
PPAP/Safety Case:
功能安全案例框架建立在 IATF 16949 生产零部件批准流程(PPAP)之上,包括所有安全论点和工作输出。这些都存储在配置管理系统的专用功能安全部分。这种方法确保了所有与安全相关的方面都是可追踪且有文档记录的,符合最高的质量和安全标准。